How Easy is It to Cut Steel
How to Cut Steel: Different Methods Explained
March 23, 2022 | Categorised in: Steel 101
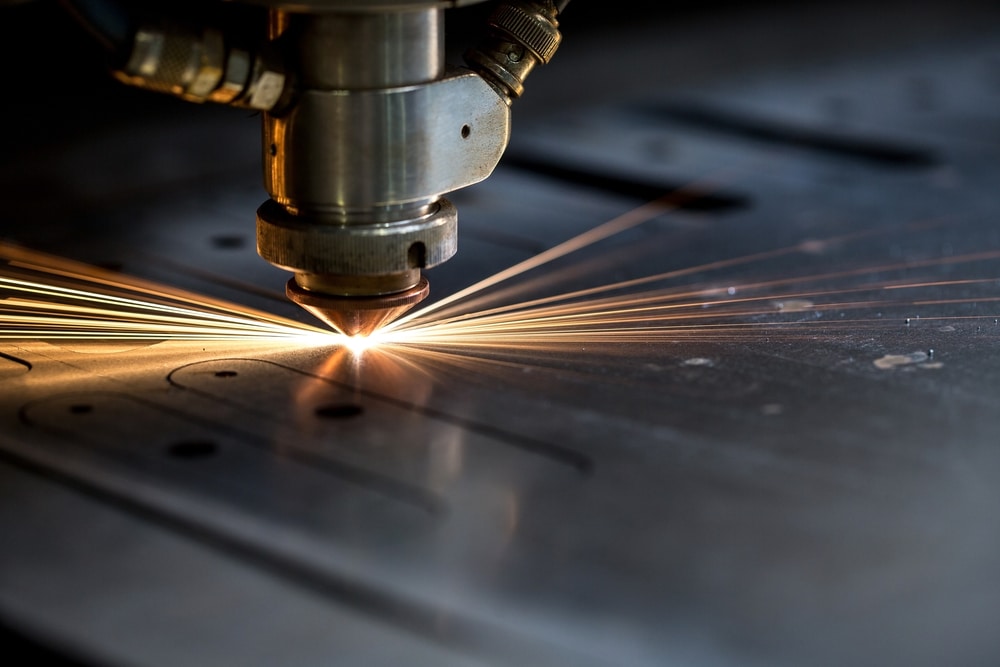
Steel cutting is a critical step in steel fabrication , but why does steel need to be cut after it's produced and why are there different ways of cutting it? There are a number of factors that inform these decisions, so let's go through them.
Why does steel need to be cut?
Steel products generally can be bought in standard sizes or dimensions, but many projects require different specifications for particular uses or situations. This is where steel cutting comes in handy and allows for even further modification and refinement of the steel you receive. For most projects using structural steel , cutting to size is a must-have.
Major techniques for cutting steel
Depending on certain aspects of the steel being cut as well as the tolerance or required precision of the cuts being made, different methods might be used. The five primary methods used today are:
Laser cutting
Typically employed for thinner steel (less than 1.25 inches), laser cutting is highly-accurate and minimizes material loss. It uses an intense beam of light focused by mirrors in the head of the laser cutter to direct the extreme heat at the steel and melt it along predetermined cutting paths. However, laser cutting is also slower than some of the other cutting methods and can heat up the surrounding area of the cut, leading to warping or thermal stress.
Waterjet cutting
As its name suggests, waterjet cutting uses high-pressure water (or a mixture of water and an abrasive substance, such as garnet or aluminum oxide) to quickly erode and cut away steel. Unlike laser cutting, there is no heat distortion from this method and it can cut thicker pieces of steel , up to 8 inches. Because of this, waterjet cutting is also the most expensive type of steel cutting due to its versatility, accuracy, and expensive operating costs.
Plasma cutting
Plasma, or superheated ionized gas, is directed through a fine nozzle at steel (or other electrically conductive materials) and uses an electric arc that passes through the conductive plasma to melt the steel. The high-pressure gas from the nozzle then cuts through the molten steel and blows it away, cutting the workpiece. This method is quick, but is usually limited by a thickness of around 1.5 inches (2.5 inches for CNC plasma cutters) and can have a lower-quality cutting edge than other methods.
Flame cutting
Also called oxy-fuel cutting, flame cutting steel often involves preheating the piece around the area that's going to be cut. A torch is then used to combine oxygen and fuel gases (acetylene, propane, propylene, etc.) to oxidize and melt the metal away, cutting through large steel products . While flame cutting is slower than plasma cutting due to the preheating process, it's generally the most cost-effective method and can cut through steel as thick as 48 inches. Flame cutting can also be less finely-tuned than other methods — but at these sizes, the accuracy and tolerances are much less delicate and strict. Most of the steel cutting that we perform is flame cutting.
Sawing
The final method of cutting steel is also the most basic, and that's using a circular or band saw for the process. Saw cutting steel can allow for close tolerances, as well as reducing the waste material produced.
Get your steel cut today
Service Steel has the versatility to cut your steel products to size at a cost-effective rate and for any of your project's needs. Whether you need flame cutting , sawing, or other finishing services such as galvanizing or impact testing , we can quickly supply you with the steel you need.
Source: https://www.servicesteel.org/resources/how-to-cut-steel
0 Response to "How Easy is It to Cut Steel"
Post a Comment